塑料注射成型在塑料制品中占有很大比重,在傳統(tǒng)的注射模設(shè)計及加工方法中,有些設(shè)計參數(shù)只能依靠有限的資料和經(jīng)驗確定,但塑料注射成型過程十分復(fù)雜,單純依靠傳統(tǒng)的經(jīng)驗設(shè)計和制造方法已很難滿足生產(chǎn)質(zhì)量要求。
注射模CAD/CAE/CAM的重點(diǎn)在于注射產(chǎn)品的造型、模具設(shè)計、繪圖和數(shù)控加工數(shù)據(jù)的生成,而CAE包含的工程功能則更廣泛。CAE將工程設(shè)計、試驗、分析、文件生成以及制造貫穿于產(chǎn)品研制過程的每個環(huán)節(jié),以指導(dǎo)和預(yù)測產(chǎn)品在構(gòu)思和設(shè)計階段的行為。CAD/CAE/CAM的集成化從根本上改變了傳統(tǒng)的模具生產(chǎn)方式。采用幾何造型技術(shù),注射產(chǎn)品一般不必進(jìn)行原型試驗,產(chǎn)品形狀能逼真地顯示在計算機(jī)屏幕上,并能借助于彈性力學(xué)有限元軟件對產(chǎn)品力學(xué)性能進(jìn)行測定。CAD/CAE/CAM有以下幾個優(yōu)點(diǎn):①提高生產(chǎn)率;②提高質(zhì)量;③縮短周期;④有效地利用了有限地人才資源;⑤有利于技術(shù)資料儲備,價值提高。
隨著塑料注射成型CAE技術(shù)在模具、汽車、家用電器、儀器儀表等行業(yè)中的廣泛應(yīng)用,目前已有許多外國公司出售商品化的流動模擬軟件,如澳大利亞的模具流動公司的M0LDFIDW,美國AC―TECH公司的C本文采用MPI模擬分析軟件對某注塑件進(jìn)行流動模擬分析,并以此為例介紹模具CAE技術(shù)在注塑模設(shè)計中的應(yīng)用。此軟件可以幫助模具設(shè)計人員解決以下問題:①通過最佳澆口位置分析,可以確定澆口的位置和數(shù)目;②預(yù)測熔接痕的位置,并通過比較確定更為合理的工藝參數(shù),使熔接痕處在理想的位置;③預(yù)測可能存在的泡孔位置,以確定排氣槽的開設(shè)位置;④優(yōu)化成型工藝參數(shù)1模擬分析過程*:2002― 0卜21;基金項目:云南省自然科學(xué)基金資助項目(項目編號:2001E0016M)。
模具分析模型的建立為該零件的三維實體模型。由實體模型建立的該注塑件的有限元分析模型如所示,在分析中采用雙層面網(wǎng)格形式,有限元分析模型數(shù)據(jù)為:面單元數(shù)=4256節(jié)點(diǎn)數(shù)=2126。澆口位置的確定及流動分析為了更清楚的說明應(yīng)用CAE軟件進(jìn)行注塑流動分析的優(yōu)越性,在本文分別對三種不同澆口位置進(jìn)行分析,以做比較。
*ZY*125型號注塑機(jī),其技術(shù)規(guī)格為:注射壓力=119.00MPa;鎖模力=92.00t.塑件所用材料為ABS,相關(guān)參數(shù)為:塑料熔融溫度=230.00 *C;模具溫度=60.00 *C為比較方便,三種澆口位置的最大充填壓力、注塑時間取為相同值,即:最大充填壓力=54.60MPa;注塑時間=5.00s.澆口居右(記為位置1)時的流動分析:實際注射時間= 5.09s;最大補(bǔ)縮壓力=58.85MPa;塑料最大流動速率=1.32瓜3“;流動前鋒最低溫度=150.19 1;流動前鋒最高溫度=230.081.澆口居中(記為位置2),并做流動分析:實際注射時間=5.07s;最大補(bǔ)縮壓力=60.45MPa;塑料最大流動速率=1.32m3/s;流動前鋒最低溫度=164.67C流動前鋒最高溫度=230. 3)澆口居左(記為位置3),做流動分析:實際注射時間=5.17s;最大補(bǔ)縮壓力=119.00MPa;塑料最大流動速率=1.32心3”;流動前鋒最低溫度=146.17 1;流動前鋒最高溫度=230.24。流動模擬分析結(jié)果比較不同澆口位置產(chǎn)生的氣泡在塑料熔體注射充填過程中,模腔內(nèi)除了原有空氣外,還有塑料含有的水分在注射溫度下蒸發(fā)而成的水蒸氣,塑料局部過熱分解產(chǎn)生的低分子揮發(fā)性氣體等。這些氣體若不能通過排氣系統(tǒng)順利排出模腔,將會影響制品成型以及脫模后的質(zhì)量。
在本文中,MPI分析軟件預(yù)測出塑件在充填結(jié)束時可能產(chǎn)生氣泡的區(qū)域。澆口位置不同,產(chǎn)生的氣泡的數(shù)量和位置也不同。澆口居右(位置1)時,熔體先進(jìn)入中間區(qū)域,大端部分最后充填,氣泡大部分在大端底部不利于排出。澆口居中(位置2)時部分氣泡可以在分型面處排出tM氣泡數(shù)。明顯減少澆iet口居左(位置3)時,氣泡主要集中在與分型面垂直的平面上,也不利于排出。通過流動分析軟件可預(yù)測氣泡的位置并在設(shè)計時采取有效的措施。
不同澆口位置產(chǎn)生的熔接痕一般來說,熔接痕對制品強(qiáng)度有一定影響,并且在涂漆等后處理時,熔接痕位置處較難處理,所以必須縮短熔接痕的長度。
CAE分析軟件在分析結(jié)果中分別給出了三種澆口位置的熔接痕的數(shù)量及分布。從結(jié)果可以看出當(dāng)澆口居右(位置1)時,在大端側(cè)邊緣處的熔接痕數(shù)量增多,長度增加,因為熔體充填型腔時,流程長,壓力損失大,流動前鋒溫度下降多(由分析可知,流動前鋒溫度降低了80.61*C),熔接痕處力學(xué)性能較差。澆口居中(位置2)時,熔接痕主要位于塑件大端和小端的側(cè)邊緣處,但由于熔體流程短,壓力、溫度變化要比澆口在位置1處小(由分析可知,流動前鋒溫度降低了65.42*C),熔體熔接得良好。澆口居左(位置3)時,大端側(cè)邊緣及小端邊緣處的熔接痕數(shù)量明顯增多,因為熔體在充填型腔時流程長,壓力、溫度降低得很多(由分析可知,流動前鋒溫度降低了84.07*C),所以熔接痕處力學(xué)性能差。
填充質(zhì)量澆口居右(位置1)時,型腔充滿,填充質(zhì)量較好,但由于熔接痕力學(xué)性能差,會影響塑件的強(qiáng)度。澆口居中(位置2)時,型腔充滿,填充質(zhì)量良好,塑件質(zhì)量良好。澆口居左(位置3)時,小端部分最后并未充滿,充填體積為94.63%由以上的分析結(jié)果看到,澆口居左和澆口居右兩種條件下注塑補(bǔ)縮壓力相差很大。這主要是因為在型腔充填結(jié)束后,注射壓力(此時也稱為補(bǔ)縮壓力)的作用在于對模內(nèi)熔體的壓實。壓實時的壓力在生產(chǎn)中有時等于注射時所用注射壓力的,有時也比較接近不同,如澆口居右時。當(dāng)澆口居左時,由于大端部分先充滿,所需填充壓力增大,加上冷卻作用,部分區(qū)域冷卻凝固。而對于流動前鋒而言,隨著凝固層的增加,流動阻力增大,凝固層阻礙熔體流動致使型腔無法充滿。為克服塑料流動阻力,注塑壓力增大,在充填過程趨于結(jié)束時注塑壓力突變至注塑機(jī)最大注塑壓力。
實際生產(chǎn)驗證在實際生產(chǎn)中,當(dāng)澆口居左(位置3)時,會出現(xiàn)充填不滿的現(xiàn)象,出現(xiàn)大量廢品,這與模擬預(yù)測結(jié)果相一致。后經(jīng)工廠工藝改進(jìn),澆口位置由位置3改到位置2附近,產(chǎn)品質(zhì)量合格,模擬預(yù)測結(jié)果與生產(chǎn)結(jié)果相吻合。除此之外,模擬預(yù)測的氣泡和熔接痕的位置也與實際生產(chǎn)相吻合。
結(jié)束語一直以來,塑料制品成型設(shè)計都是憑借一定的基礎(chǔ)知識和工作經(jīng)驗制定的,設(shè)計方案的是否可行是在模具制造完成后,通過反復(fù)試模及返修而確定的。這樣不僅生產(chǎn)率低,而且制品的成本也大大的提高了。流動模擬技術(shù)的目的在于預(yù)測塑料熔體充填型腔的過程,計算流道、澆口和型腔內(nèi)的溫度、壓力、剪切應(yīng)變速率及剪切應(yīng)力的分布,并將結(jié)果以圖表及著色圖的形式顯示出來。用戶可以直接在屏幕上看到不同工藝條件、不同設(shè)計方案下的成型過程的差異,通過比較選擇最佳的成型方案,并且可以從分析結(jié)果預(yù)測可能出現(xiàn)的成型缺陷,提出相應(yīng)的對策,以減少試模、修模次數(shù),縮短模具制造周期,降低成本提高產(chǎn)品質(zhì)量。
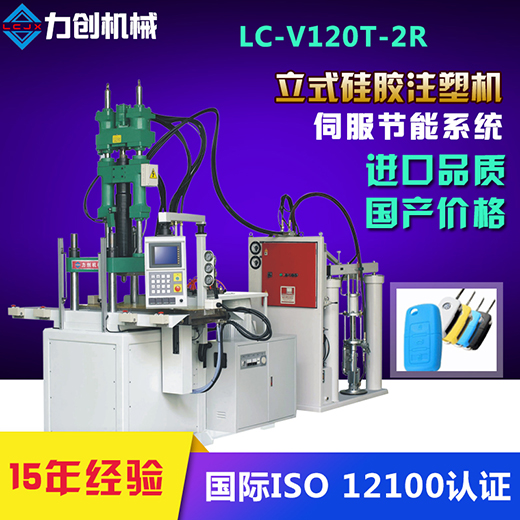
力創(chuàng),專注制造立式注塑機(jī),雙色注塑機(jī),小型注塑機(jī),全自動注塑機(jī),立式成型機(jī)